Put People First With Telematics
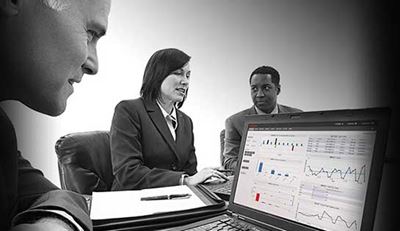
Certain day-to-day goals of warehouse operations managers have remained constant for years – namely, reducing total costs while creating value in the operation. In the past, operations managers measured value by how quickly goods could be moved from one point to another. Although that is still important, operations managers today are finding that more information is needed to see the bigger picture.
Certain day-to-day goals of warehouse operations managers have remained constant for years – namely, reducing total costs while creating value in the operation. In the past, operations managers measured value by how quickly goods could be moved from one point to another. Although that is still important, operations managers today are finding that more information is needed to see the bigger picture. Overall productivity is actually dictated by product damage and operator productivity and protection. A shift in any of these things could affect the bottom line. In today’s warehouses, the focus is not only on operator speed but also on how efficiently operators go about their work.
Since 1969, federal law has said that all operators must be trained and evaluated before operating a lift truck. Comprehensive forklift training programs have successfully reduced accidents caused by heedless lift-truck operating practices. The forklift industry has come quite far in its efforts to keep truck operators in good working conditions, and the latest advancements involve telematics. Fleet telematics consists of technology that allows an operations manager to monitor the movements, status, and behavior of a powered industrial vehicle and its operator and to make fact-based decisions.
The first fleet management systems delivered spreadsheets of raw data that required sorting and summarizing – a very time-consuming task. Modern telematics systems use dashboards that deliver real-time data to provide in-depth insights on operations, enabling managers to make quick and informed decisions. Trucks now have multiple sensors that communicate wirelessly with these systems so data can be delivered instantly and managers can address issues as they occur.
Many operations managers know that telematics systems provide an excellent tool for weeding out extra costs. Telematics systems can help managers ensure that a fleet is the right size and is tailored to meet specific needs and can refine maintenance schedules to avoid overspending and detect minor issues before they turn into expensive repairs. Although most companies track lift-truck fleet data in this way, not all of them track equipment- and driver-specific data – and in doing so, they neglect valuable employee management tools at their disposal. Today's telematics systems offer instant data delivery, cameras that take pictures and video, and direct communication between drivers and management. These allow operations managers to to see a bigger and more multifaceted picture, bringing them closer to their drivers in a number of ways. Consider these applications:
- Tracking improvement: With detailed and intuitive data measurement, it is easy to see improvements in productivity over long spans of time. Driver-specific monitoring even allows managers to see who is performing well to aid in identifying and sharing best practices with the team. On the other hand, it is also easy to find opportunities for improvement.
- Operator verification: When an operator enters a code or badge onto a truck, the telematics system will verify whether the operator’s certification is up to date and whether the operator is approved to operate the vehicle. If not, the truck will not start.
- Truck checklists: The telematics system on a truck can display a pre-operational electronic checklist for truck operators to complete before the truck can be put into use.
- Impacts recorded: If the truck makes an impact with racking or another truck, it can report the date, time, operator name, force level, and truck speed and can record video of the incident. This provides useful information for identifying whether further training is required or if a change is needed in the warehouse environment, such as in high-risk zones.
- Truck and operator utilization: Telematics systems can report hours that trucks have been in use by specific operators so operations managers can see whether certain trucks are underutilized or unnecessary and whether operators are spending too much or too little time on the truck. The systems also can track and report on specific operator tasks for a more-informed view of productivity.
Operations managers have the tasks of managing their fleet and, of more importance, taking care of their employees. Telematics helps them to do that in the fairest way possible: with all the facts and insight to make an informed decision. Whether to prove that an employee deserves recognition for great work, to identify that further training is required, or to keep drivers up to date on certification, telematics is an ideal tool to help managers put their people first.
Submitted on Tue, 12/13/2016 - 11:13
Plant Services, Today's Optimized Facility
Read the full post: http://www.plantservices.com/blogs/todays-optimized-facility/put-people-first-with-telematics/